Super Alloys
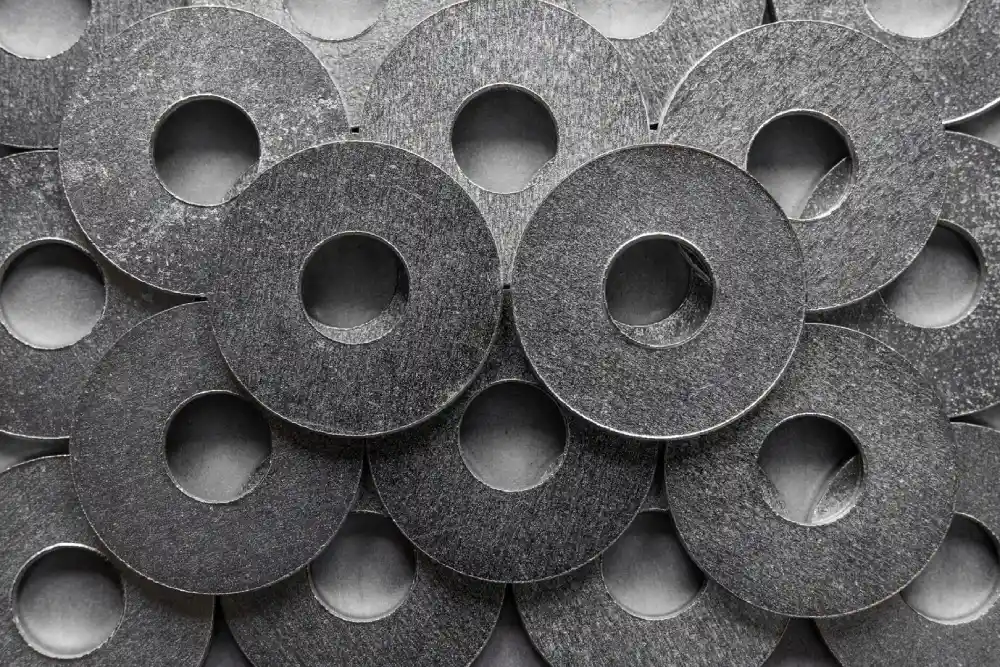
India is fast developing economy with population over 120 million with vast border. To meet the growing demand of our population and protect our border, growth of technology is inevitable. The growth of technology is relevant to sectors like Biomedical, Aerospace, Petrochemical, Thermal and Nuclear Plants, Defense, Arnament, Transport etc. To attain high level of perfection in this sectors depends, on availability of stringent quality of rawmaterial. As on date most of raw material is imported.
Government of India has embarked upon ambitious program of self reliance through make in India program. Sunflag widely accepted as marque company in supplying high quality material to automobile and general Engg industries wish to enter this high tech area. The fast developing electrical vehicle technology may also require these advanced high tech material in high volume.
These hi tech material are used in making Aircraft Parts, Bio Medical Implants, Industrial and Vehicle Gas Turbines, Super Critical Power Plants Parts, Space Vehicles and Rocket Engines, Submarine Parts, Nuclear Reactor, Missiles and Arnaments etc.
The high-performance high-tech alloys required by these industries are required to be operated at a load and temperature above 500 degrees centigrade with resistance to oxidation and environmental attack, which are usually prevalent at this temp. Hence the raw material used for this high sector requires low level of impurities and meets stringent spec.

In nature, we rarely come across very pure material and it contains metallic impurities like lead, bismuth, etc, non metallic impurities like sulphur. phosphorous etc, residual gases like oxygen. hydrogen and nitrogen and nonmetallic impurities like oxides, nitrides. Sulphide etc.
The above impurities considerably reduced in conventional technology of arc furnace, AOD, LRF and VOD and the low level of impurities required by these hi-tech industries can be achieved only by melting at Vacuum Induction Melting [VIM], Electro Slag Refining [ESR] and Vaccum Arc Re-melting furnace [VAR] etc apart from other specialised melting.
Sunflag has put up VIM, ESR, VAR facility at Bhandara Plant near Nagpur. These equipment have latest technology and supplied by the World Leaders in this field, Sunflag also have tie up with DAIDO Japan, who are well known have equity participation with Sunflag. DAIDO also provide inputs for improvement in the technology.
Sunflag other facilities include Concast, Blooming Mill, specialised Rolling Mill, Heat Treatment facilities and Bright Bar and Centerless Grinding Facility.
To test this high-tech material, most modern labs are equipped with good analytical instruments, metallographic equipment, and mechanical testing equipment for testing RT, LT and HT specimens. Online Phase Arrey Machines for testing UT, eddy current, MPl and FPT tests also available to test the product to various national and international standards
Sunflag has trained manpower who have specialised skill to operate these most modern equipments & control.
Sunflag Hi Tech Grades
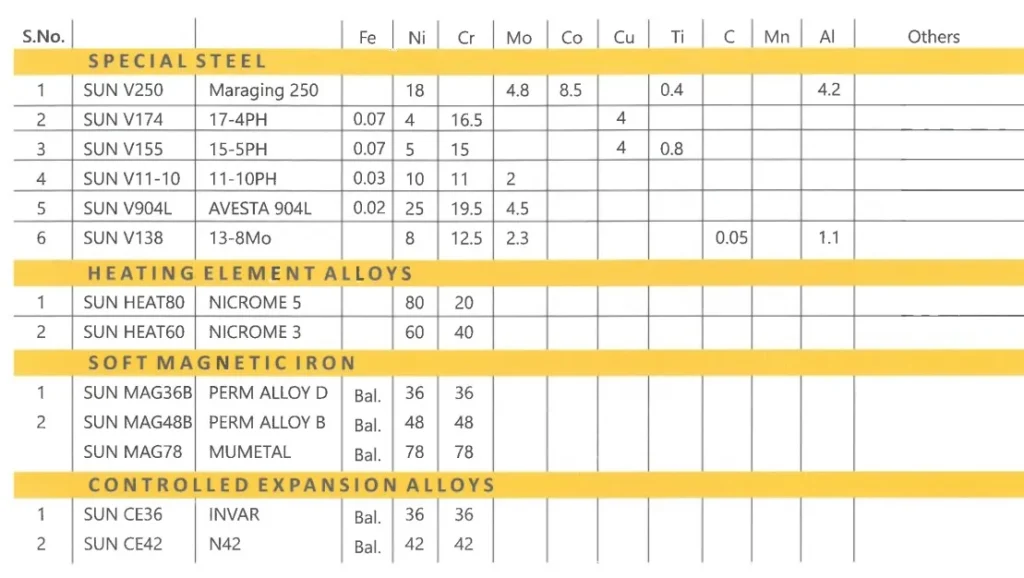
Sunflag Hi Tech Grades
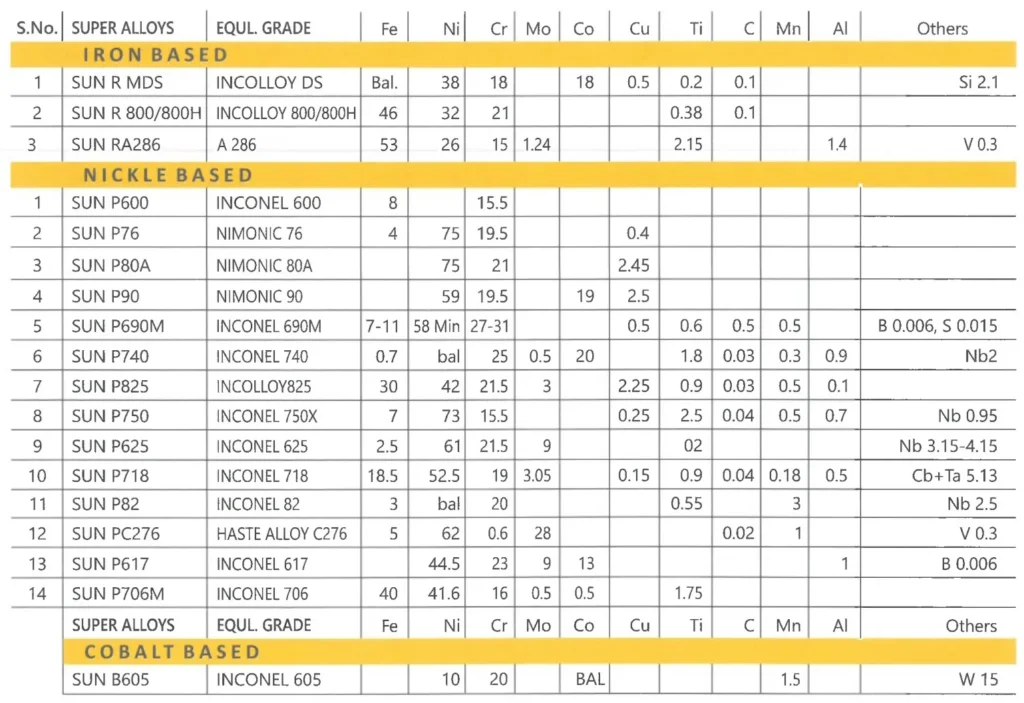
Typical Properties Of Some Grades
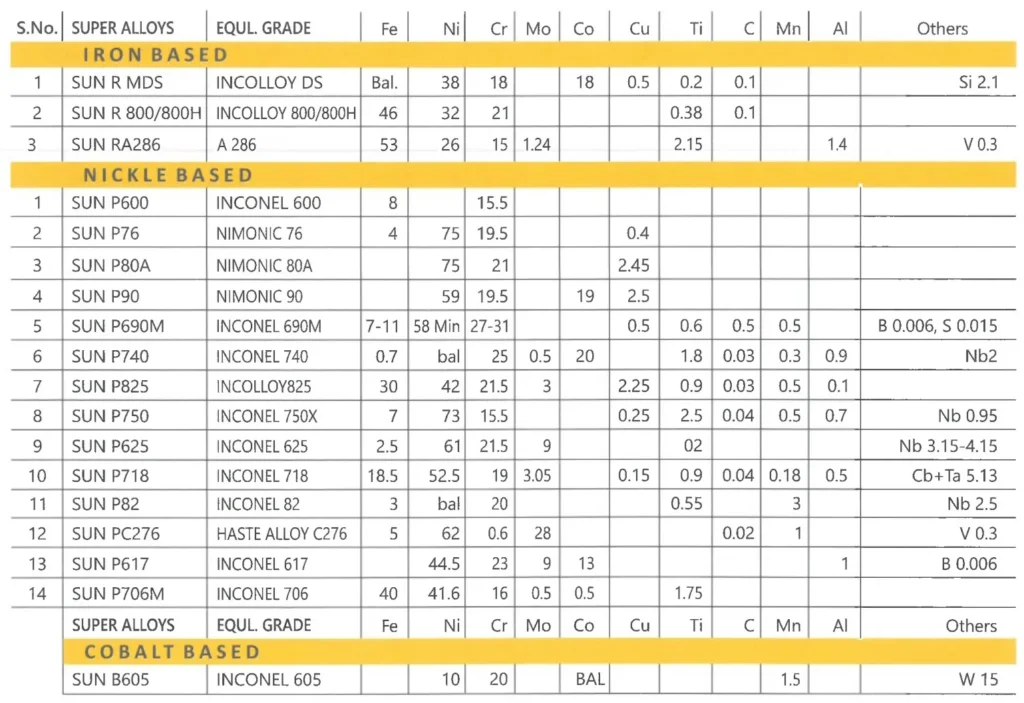
Typical Properties Of Some Grades
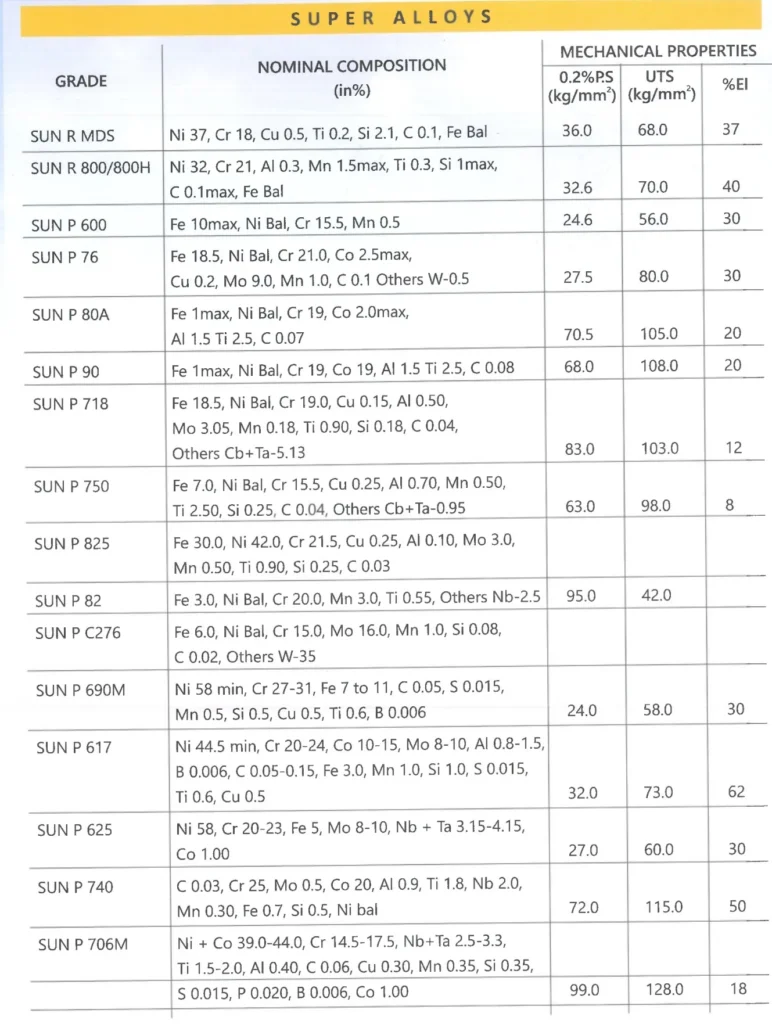