Excellence in theSteel Industry
Sunflag Iron and Steel Co. Ltd. is a prestigious unit of the SUN FLAG GROUP. The plant is located in the central part of India at Bhandara, Maharashtra & it is 70 kms from Nagpur. The plant has a capacity to produce 500,000 tonnes per annum of high-quality special steel using liquid pig iron and sponge iron as basic inputs.
Sunflag steel was incorporated as a Public Ltd Company in the year 1984. Started as a Spring Steel producer, the company has been continuously upgrading its Manufacturing and Quality Assurance Facilities.
The main processes at the plant are,
Super Alloy Division
Sunflag Steel, we specialize in crafting superalloys that define strength, durability, and resistance to extreme conditions. Our superalloys are engineered to perform in the most challenging environments, from aerospace to power generation, offering unparalleled performance where it matters most.
Electro Slag Refining (ESR)
Vacuum Induction Melting (VIM)
Vacuum Arc Remelting (VAR)
ISO-Certified Manufacturing & Quality Assurance
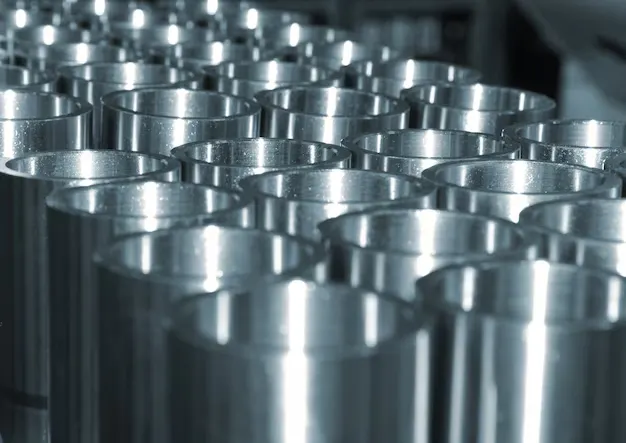
The company acquired technical skills to produce a variety of steel grades conforming to various national & international specifications and customer-specific requirements in categories of Carbon Steels, Alloy Steels, Free & Semi Free Cutting Steels, Micro-Alloyed Steels, Stainless Steels, Spring Steels, Valve Steels, Bearing Steels, Cold Heading Quality Steels, Tool Steels, High Strength Steels and Super Alloys (Special Steels, Heating Element Alloys, Soft Magnetic Iron, Controlled Expansion Alloys, INCONEL, INCOLLOY, INVAR, NIMONIC, HASTE Alloy).
Products are available in various profiles – Round Bars, Round Cornered Squares in straight bars, Round & Hexagonal wire Rods as coils, Hexagonal and Flat sections straight bars, as well as Bright Bars (Peeled/Drawn/Ground bars).These products are mainly used for the manufacture of Automotive Transmission Gears, Drive Shafts, Steering System, Bearings, Exhaust System and Engine Components through hot forging, cold forming and machining operations.
Strategic Collaboration and Innovation
Our products also being supplied to Indian Railways, Ordnance Factories, Power Sectors & other General Engineering areas for the manufacture of critical application components. In order to meet the market demands for new grades/applications, improve existing processes and products and to support our esteemed customers in their efforts for localization of their steel requirements, Sunflag Iron & Steel Co. Ltd. has entered into Technical Collaboration with Daido Steel Company, Japan in the year 2010. This association has proven useful for improvement in Production Process and Product Quality, Development of New Grades, Localization of Steel by the Automobile OEMs.
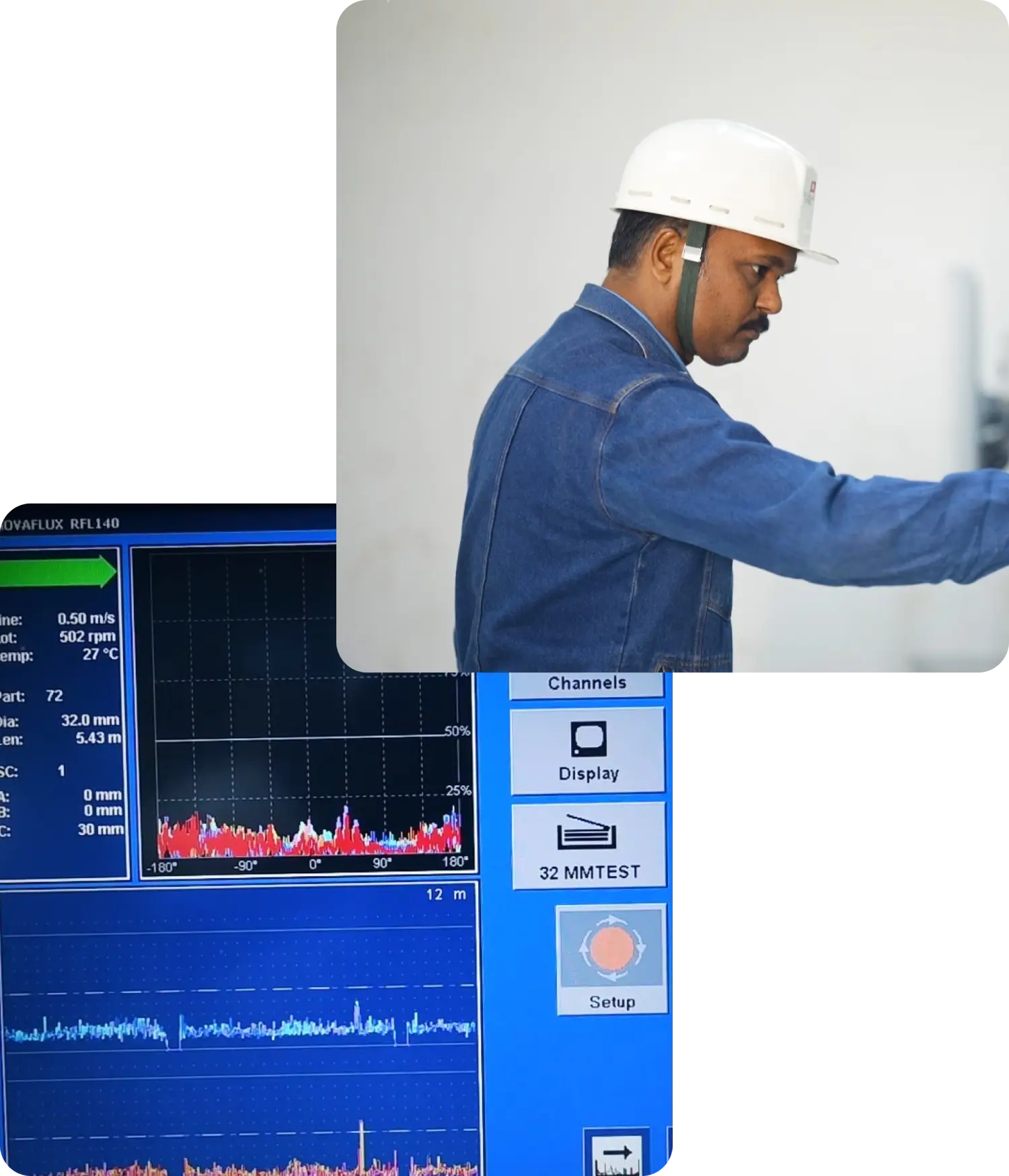
ISO-Certified Manufacturing & Quality Assurance
Apart from catering to the Domestic steel requirements, Sunflag Steel also exports to South East Asian Countries, Middle Eastern Countries, European Countries and The United States. At Sunflag, Steel is produced using 100% Iron Ore as a basic raw material input. No scrap is sourced from outside. The steel has very low contents of the tramp element and is free from radioactive contamination or other harmful and hazardous chemicals.
The Manufacturing and Quality Management systems has been standardized and certified under ISO 9001, IATF 16949, ISO 14001, OHSAS 18001, AD-2000-Merkblatt WO. The in-house testing laboratories are certified under ISO/IEC 17025 Standard by the National Accreditation Board for Testing and Calibration Laboratories (NABL).