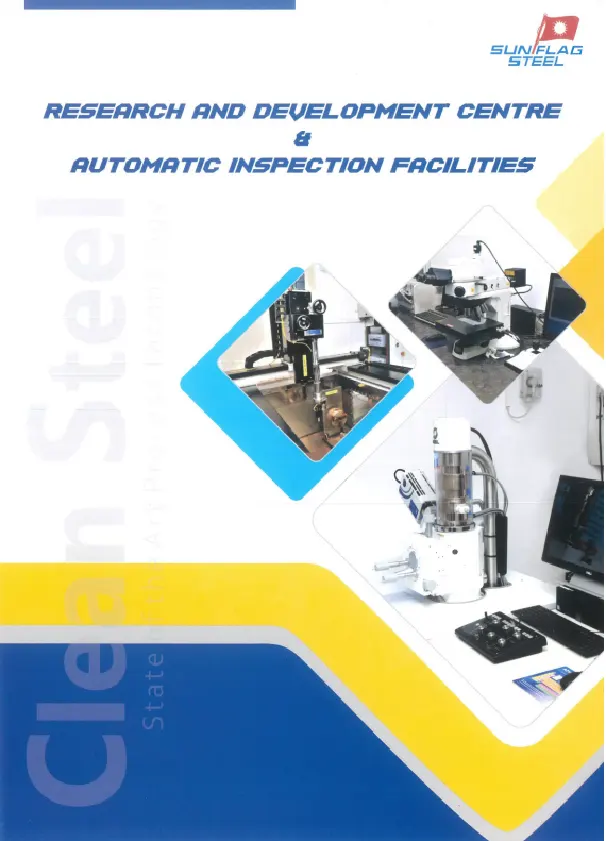
Research And Development
R & D division of Sunflag Iron Steel Co. Ltd. Plays a pivotal role in retaining and consolidating Sunflag’s leadership position in the automobile industry.
R&D focus on the development of new steel grades, process improvement, continuous up-gradation of Quality, and Customer Satisfaction through customized products matching their specific requirement.

Tool Steels
Tool steels are high quality steels made to controlled chemical composition and processed to develop properties useful for working and shaping of other materials.The carbon content in tool steel may range from as low as 0.1% to as high as more than 1.6%. They are alloyed with elements such as Chromium, Molybdenum,Vanadium Tungsten etc.
At Sunflag Tool Steels are produced through specially designed steel making process via Electric Arc Furnace followed by Ladle Refining and Vacuum Degassing and processed through ESR / VAR for ensuring homogeneous properties &Ultra clean material. Stringent control is practiced during designing of chemical composition and other process parameters during casting, rolling/forging and heattreatment.
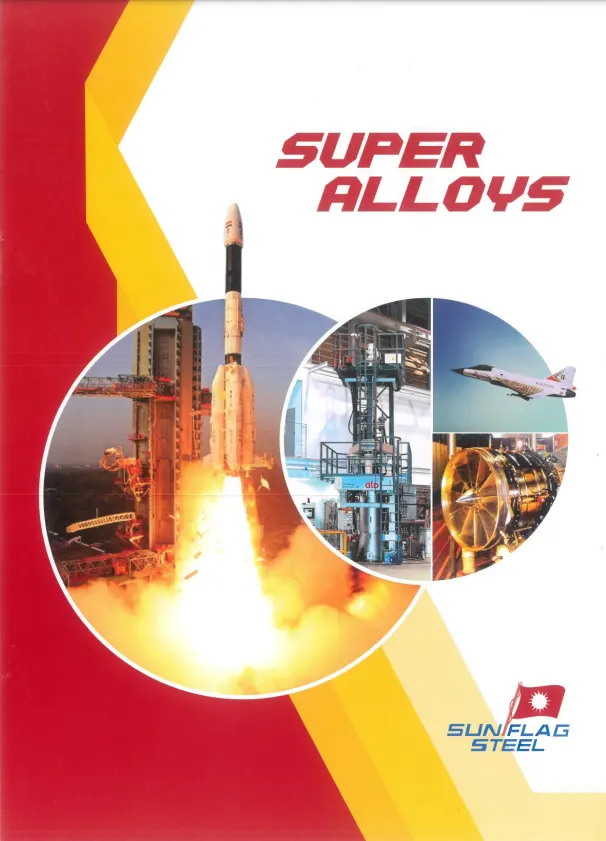
Super Alloys
India is fast developing economy with population over 120 million with vast border. To meet the growing demand of our population and protect our border, growth of technology is inevitable. The growth of technology is relevant to sectors like Biomedical, Aerospace, Petrochemical, Thermal and Nuclear Plants, Defense, Arnament, Transport etc. To attain a high level of perfection in this sector depends, on the availability of stringent quality of raw materials. As on date most of the raw material is imported.
Government of India has embarked upon ambitious program of self reliance through make in India program. Sunflag widely accepted as marque company in supplying high quality material to automobile and general Engg industries wish to enter this high tech area. The fast developing electrical vehicle technology may also require these advanced high tech material in high volume.
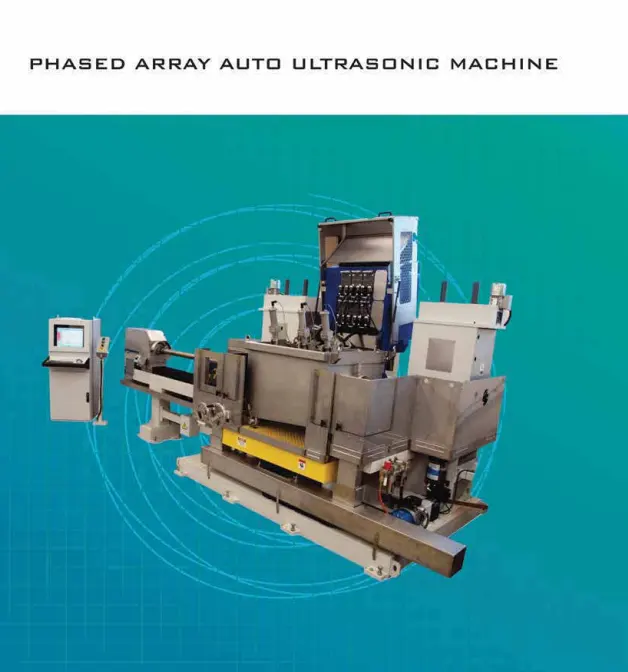
Automatic Phased Array Ultrasonic Machine
Automatic Phased Array Ultrasonic Testing (PAUT) is a non-destructive testing technique used to inspect materials for defects or irregularities. It employs an ultrasonic transducer array to generate and receive ultrasonic waves in a controlled manner. The phased array technology allows for the manipulation of the ultrasonic beam direction and focal point electronically, providing flexibility in inspecting complex geometries and detecting defects with high accuracy.
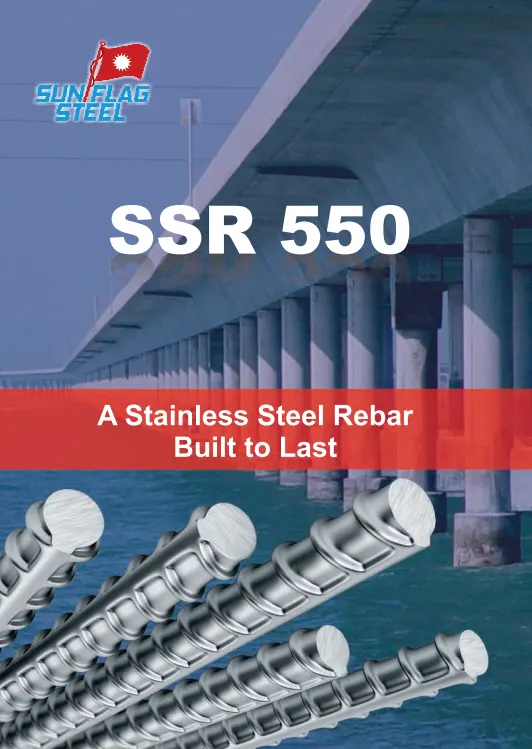
Stainless Steel Rebar 550
Stainless steel rebar is a type of reinforcement bar made from stainless steel, which is corrosion-resistant and has high tensile strength. Rebar, short for reinforcement bar, is commonly used in construction to provide additional strength to concrete structures.
In India Sunflag Iron & Steel Co. Ltd. (SlSCO) activity is divided into two business segment: Steel and Stainless Steel products and the power sector. SISCO has set—up an integrated steel plant with technical know-how and major equipments from MANNESMANN DEMAG and KRUPP of Germany. It is most modern plant, the first integrated steel plant of its kind in India with a capacity of 0.5 million tonnes per annum of rolled products, which is comparable to the best in the world. This plant produces alloy steels, special steels and stainless steels, which are also supplied to major automobile manufacturers in India and a large part of our production is exported. SISCO has its own captive thermal power plant to meet the requirements of steel plant.
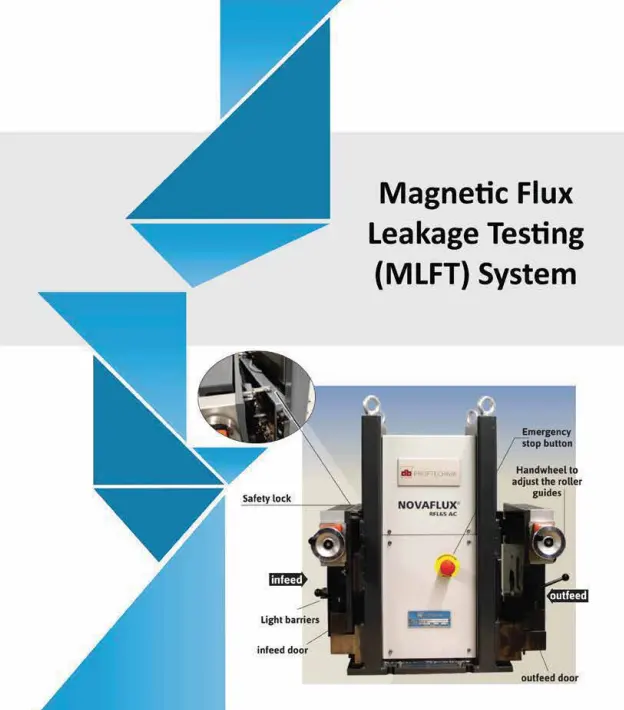
Magnetic Flux Leakage Testing System
Magnetic Flux Leakage (MFL) testing is a non-destructive testing method commonly used for inspecting the integrity of ferromagnetic materials, such as steel. The method involves the use of a Magnetic Flux Leakage Testing System, which is designed to detect and analyze anomalies or defects in the material through changes in magnetic flux.
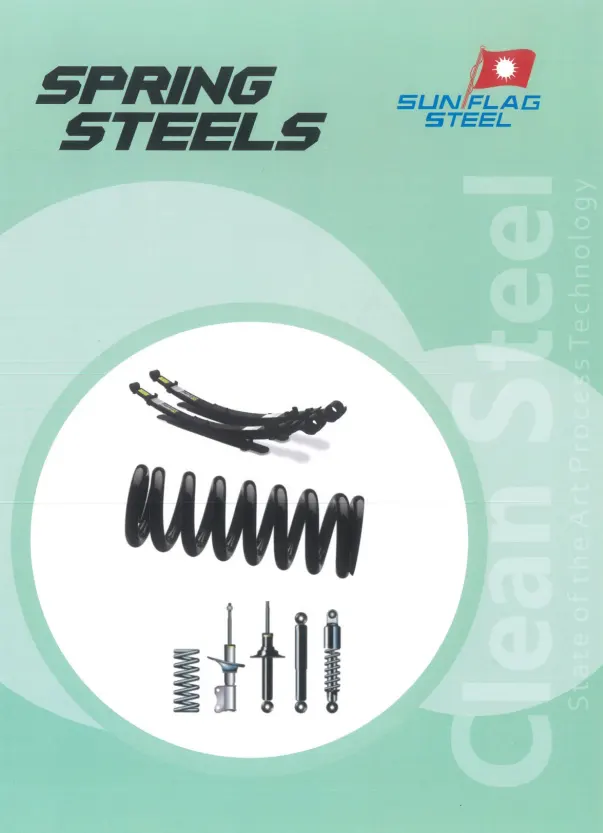
Spring Steels
Spring steels are a category of high-strength, low-alloy steels specifically designed for the production of springs and elastic components. These steels are characterized by their unique combination of high yield strength, good elastic properties, and durability, making them well-suited for applications where resilience and flexibility are crucial. Here’s a brief description of spring steels:
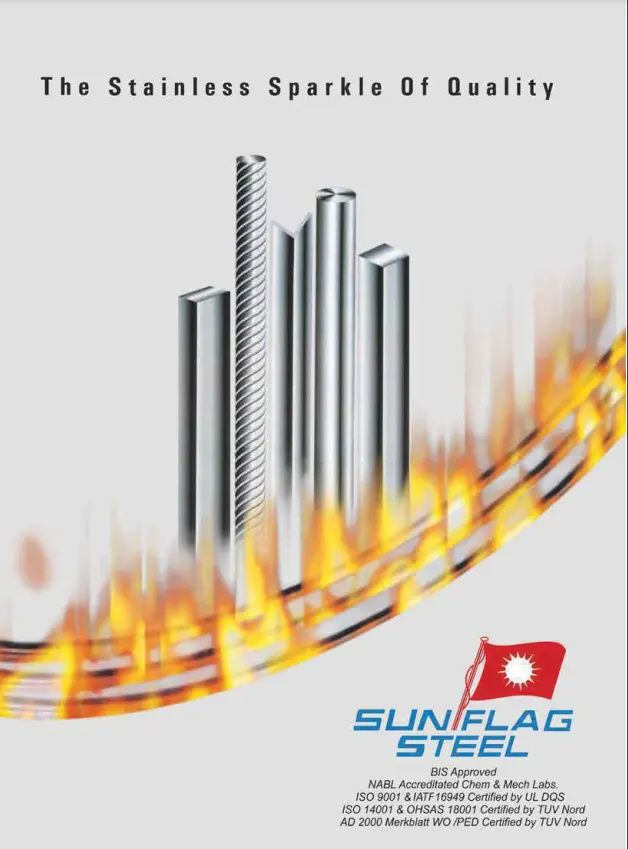
Stainless Steel
Stainless steel is steel containing 10.5% or more of chromium. which imparts it with corrosion resistant properties,by the formation of an impervious layer of chromium oxide on the surface.
Stainless Steel finds many applications,which include:
- Construction industry
- Boiler industry
- Pumps and Shaft applications
- Flanges
- Surgical applications
- Cutlery
- Weaving and Knitting Wires
- High Temperature Corrosion Resistance Chemical and Petrochemical industries
- Springs etc.
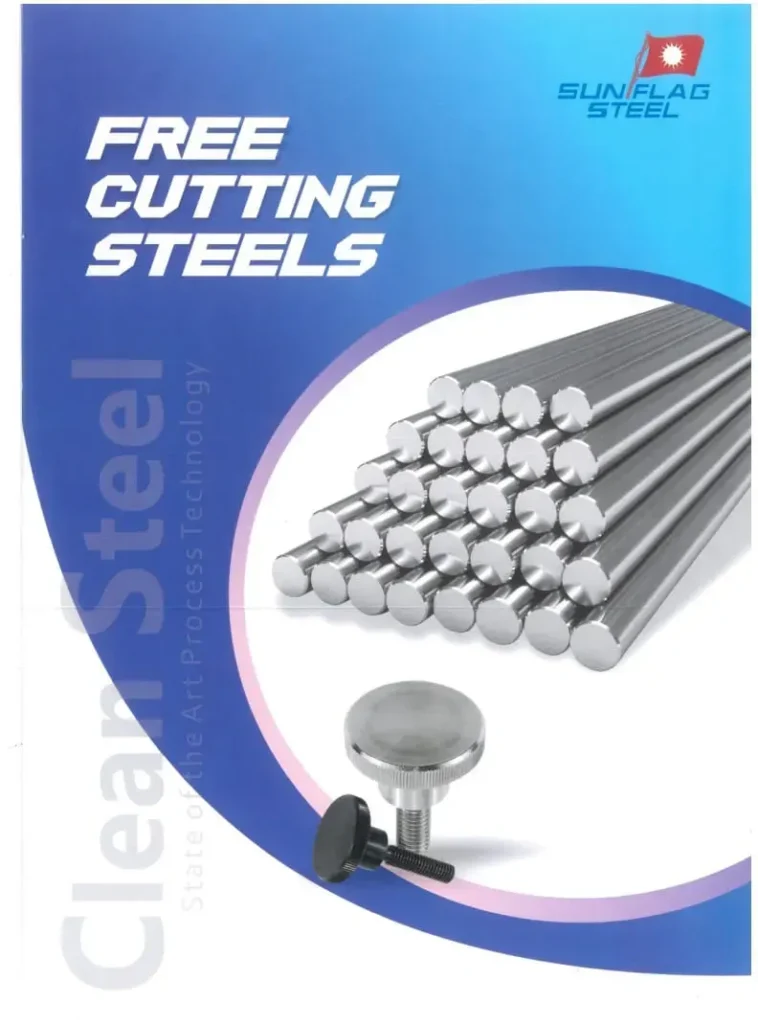
Free Cutting Steels
Free-cutting steels, also known as free-machining steels, are a category of steels that are specially designed to improve machinability during manufacturing processes such as machining, drilling, or turning. The term “free-cutting” refers to the ability of these steels to be easily machined into intricate shapes with minimal tool wear and improved chip formation.
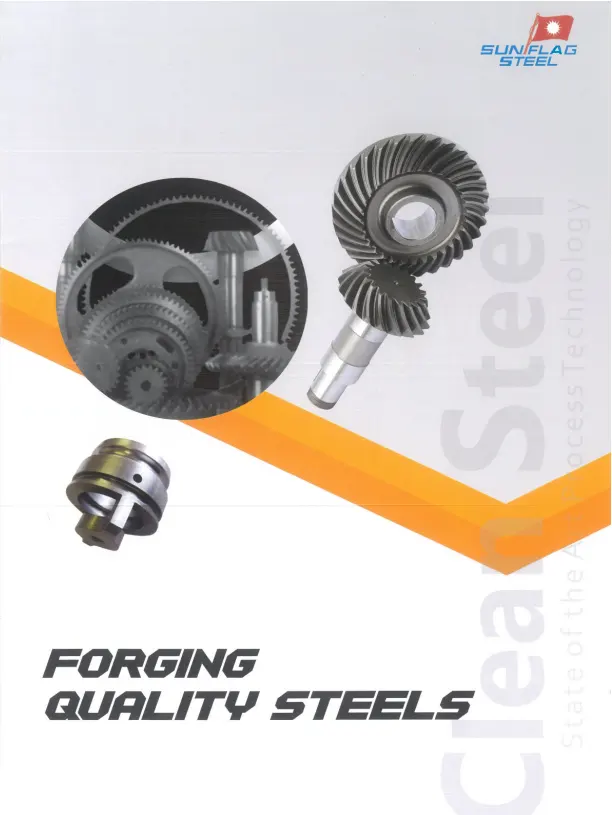
Forging Quality Steels
Forging Quality Steels are widely used in automobile, defence, railways and various manufacturing industries. Automobile industry is the single largest user of forgings. Components produced through forging are generally used in the transmission systems of an automobile where large forces get transferred between different parts.
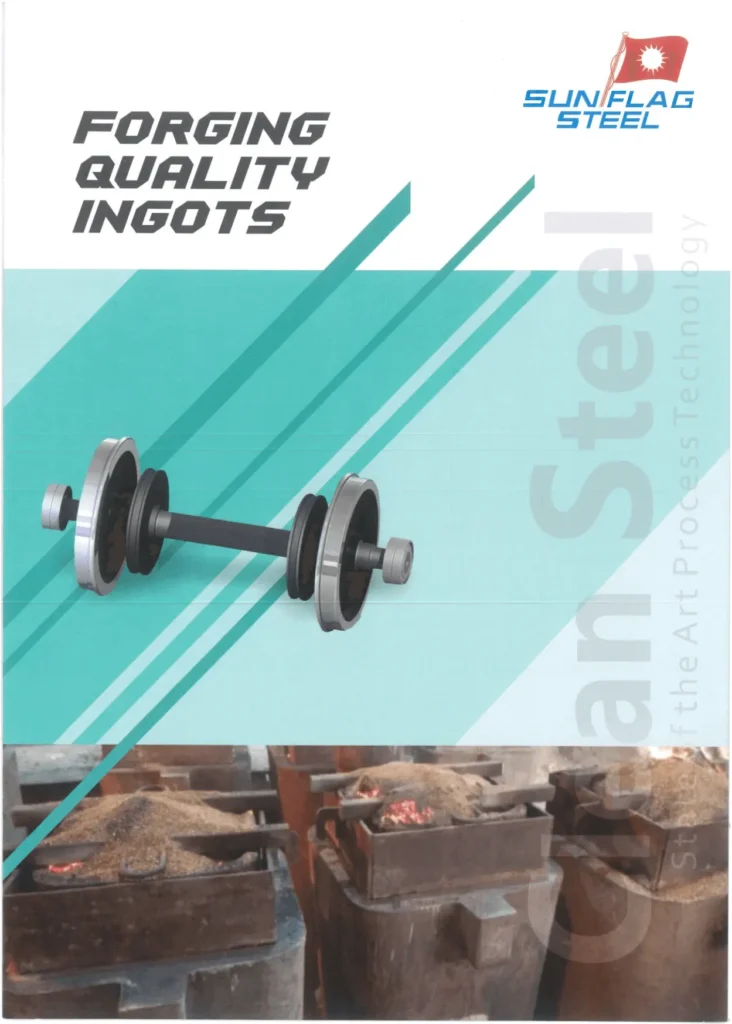
Forging Quality Ingots
Forging quality ingots are specialized metal castings produced with the intention of being used as raw material in the forging process. Forging is a manufacturing process where metal is shaped by applying localized compressive forces, typically through the use of hammers, presses, or dies. The quality of the ingots used in forging significantly influences the final properties of the forged components.
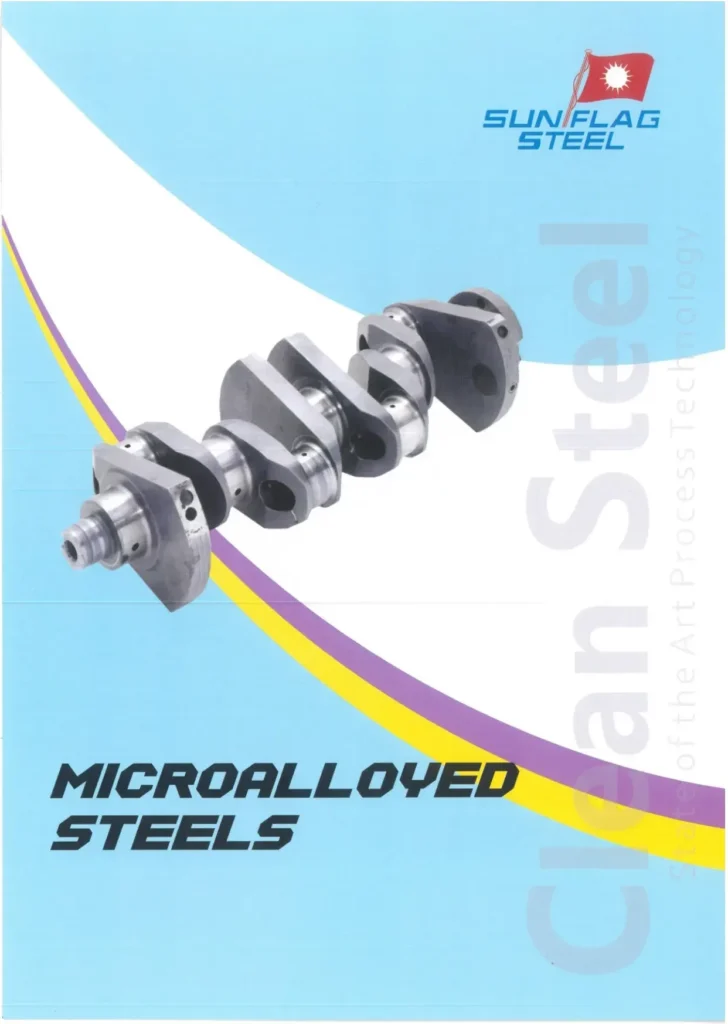
Microalloyed Steels
Microalloyed steels, also known as high-strength low-alloy (HSLA) steels, are a type of steel that contains small amounts of alloying elements, typically less than 0.5% by weight, designed to enhance specific properties without the need for complex heat treatments. These steels are known for their high strength, good weldability, and improved toughness.
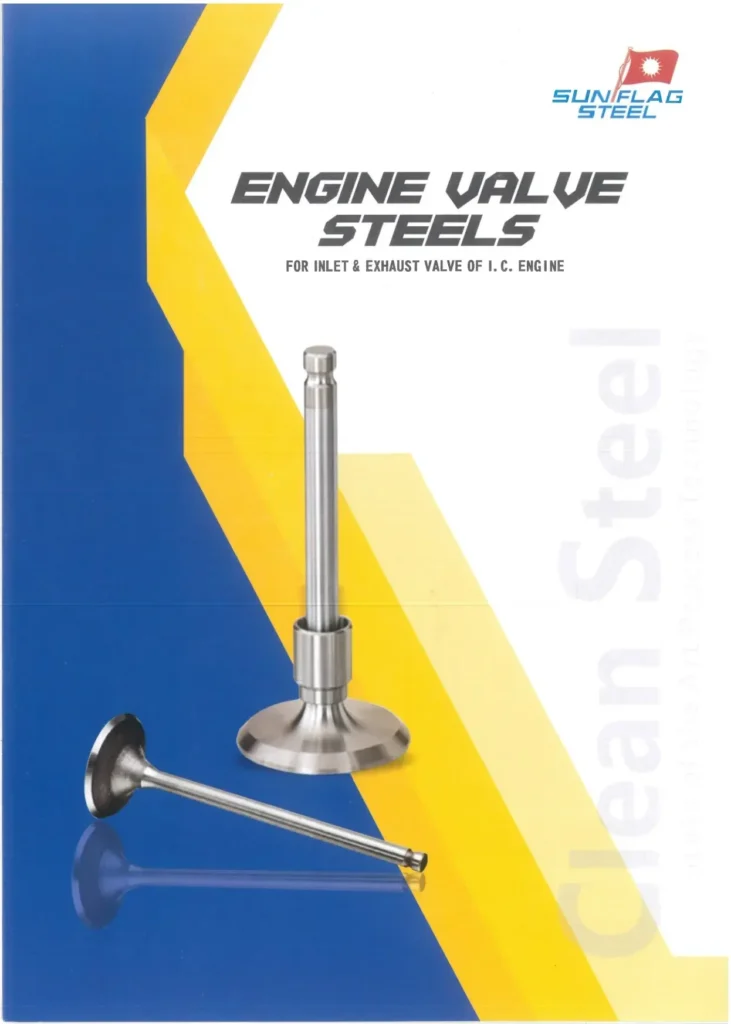
Engine Valve Steels
Engine valve steels are specialized alloys designed for the manufacturing of valves used in internal combustion engines. These steels must withstand high temperatures, severe mechanical stresses, and corrosive environments while maintaining durability and wear resistance. Engine valve steels play a crucial role in the performance and reliability of internal combustion engines.
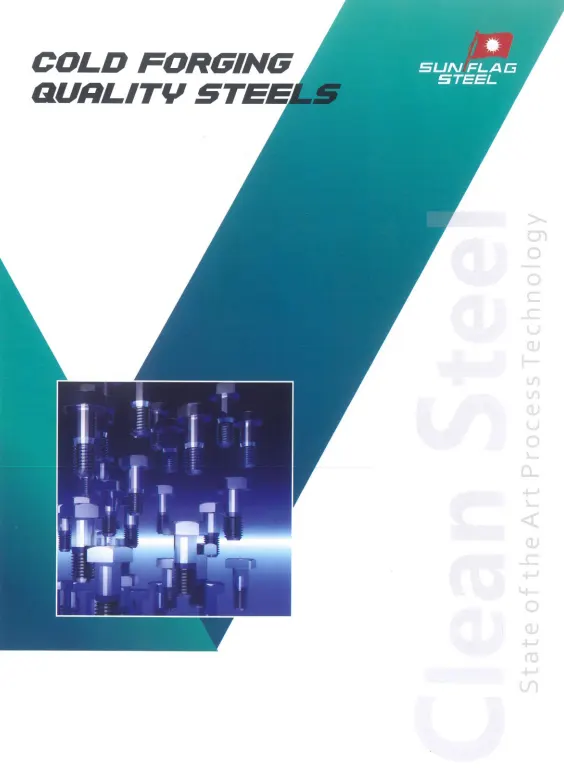
Cold Forging Quality Steels
Cold forging quality steels are specialized materials designed for the cold forging manufacturing process, which involves deforming metal at room temperature or slightly elevated temperatures. Cold forging is commonly used to produce high-strength, complex-shaped components with tight tolerances. Cold forging quality steels are selected for their ability to withstand deformation without cracking or other defects.
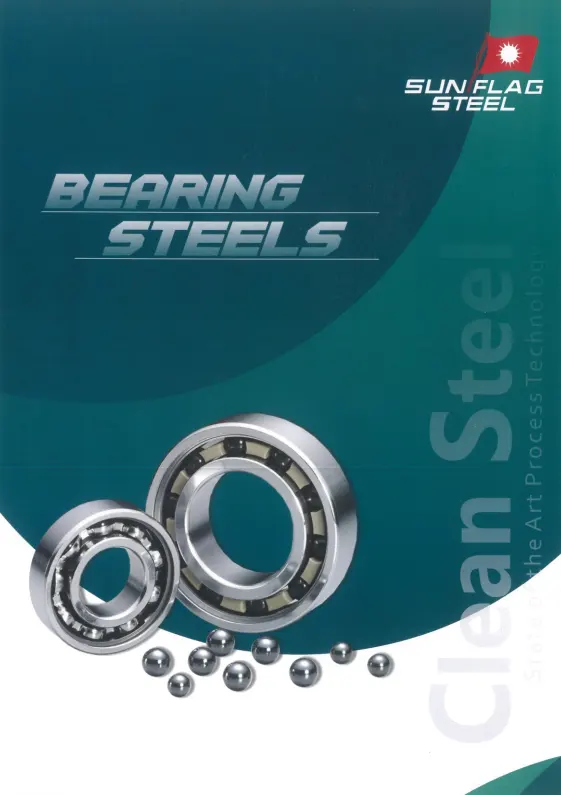
Bearing Steels
Bearing Steels are special class of low alloy steels, typically with 1% Carbon and 1.4% Chromium. In special cases, Manganese and Molybdenum are also added. These steels find applications in automobiles, railways, earth moving, defense, aircraft, power generations, compressors, and other moving machinery parts. In view of the continuous fatigue strain during service, this steel and its components demand a high level of process discipline during manufacturing.
The components for these applications are manufactured either through hot forging route or through Spheroidized annealing followed by cold forging route. At Sunflag, all the necessary facilities for manufacturing and testing of bearing steel grades have been established. Various controls are exercised during manufacturing, right from selection of raw materials and ferro alloys required to meet the stringent quality parameter of the various customer.
- Fatigue Life
- Uniform heat treatment response
- Compact Structure with uniform grain flow and fine grain size
imparting high impact toughness